A técnica de tempo de percurso da onda difratada (ToFD) em soldas
Redação
Muitos ensaios não destrutivos (END) são utilizados para a detecção, dimensionamento e avaliação de defeitos em juntas soldadas, sendo o ultrassom e a radiografia os mais relevantes. Apesar de o ensaio radiográfico ter uma empregabilidade elevada, o ensaio ultrassônico, devido à sua sensibilidade de detecção a descontinuidades tem se destacado atualmente como o principal método de validação de estruturas soldadas. Outra aplicação recente do ultrassom é a caracterização de tensões residuais em soldas. Essas tensões residuais são originadas principalmente de tensões de compressão e tração impostas pelos subsequentes ciclos térmicos de aquecimento e resfriamento de soldagem a que são impostas a zona fundida e adjacências. Dentre as técnicas ultrassônicas convencionais, o método pulso eco detecta descontinuidades presentes no material através dos ecos de reflexão provenientes das mesmas. Entretanto, assim como as demais técnicas tradicionais, esse método baseia-se na hipótese de que a descontinuidade possui uma orientação favorável à reflexão. Visando superar essa dificuldade, a técnica ToFD (Time of Flight Diffraction) vem obtendo êxito na inspeção de juntas soldadas de estruturas, uma vez que se baseia no dimensionamento e capacidade de detecção através dos ecos difratados na extremidade superior e inferior da descontinuidade. Esta técnica tem as vantagens de precisão no dimensionamento de defeitos, alta probabilidade de detecção de descontinuidades, com uma baixa taxa de falsas indicações. A sua rapidez e o baixo custo quando comparada a técnicas radiográficas tem justificado o emprego da técnica em aplicações em serviços. Conheça a ToFD para o ensaio de ultrassom de juntas soldadas em materiais metálicos com espessura maior ou igual a 6 mm. Destina-se principalmente ao uso em juntas soldadas de penetração total de geometria simples em chapas, tubos e vasos, onde tanto a solda quanto o metal de base são de aço de baixa liga.
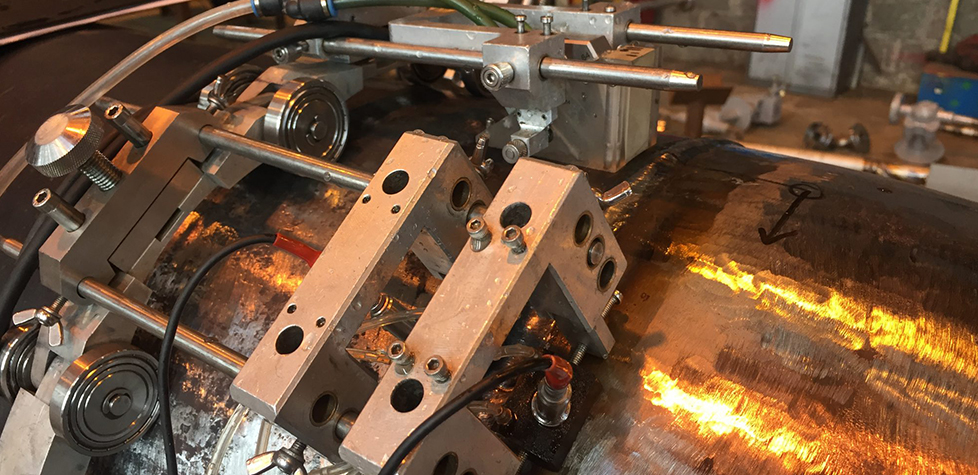
Da Redação –
Devido as dificuldades encontradas nas técnicas ultrassônicas convencionais, novos métodos de inspeção foram desenvolvidos como alternativas para detecção e dimensionamento de falhas em estruturas soldadas. A técnica ToFD se baseia no tempo de percurso da onda difratada. A técnica tem como princípio as difrações das ondas ultrassônicas nas extremidades superior e inferior de descontinuidades presentes em cordões de solda. Sua principal característica é a obtenção de medidas precisas das falhas, empregando, para isso, dois cabeçotes angulares, um funcionando como receptor e o outro como transmissor, com largura de feixe suficiente para que o máximo de área seja inspecionado (ver Fig. 6). As extremidades inferiores e superiores da interface devem gerar sinais de amplitudes aproximadamente iguais, mas em fases opostas. O primeiro sinal a chegar é o da onda lateral, enquanto os outros dois sinais são o sinal difratado da ponta da trinca superior e o sinal difratado da ponta da trinca inferior.
O arranjo ToFD é a disposição dos cabeçotes definida por suas características, como frequências, tamanho do elemento do cabeçote, angulo do feixe, modo de onda e a distância entre os centros dos cabeçotes (PCS). A PCS (probe centre separation) é a distância entre os pontos de saída de dois cabeçotes. Para as superfícies curvas, é a menor distância entre os pontos de saída. A imagem ToFD é aquela imagem bidimensional, construída pela aquisição de A-scan adjacentes enquanto movimentam-se os cabeçotes. A amplitude do sinal A-scan e normalmente representada por valores em escala de cinza.
A NBR 16196 de 05/2020 - Ensaios não destrutivos — Ultrassom — Uso da técnica de tempo de percurso da onda difratada (ToFD) para ensaio em soldas especifica a aplicação da técnica de tempo de percurso da onda difratada (ToFD) para o ensaio de ultrassom de juntas soldadas em materiais metálicos com espessura maior ou igual a 6 mm. Destina-se principalmente ao uso em juntas soldadas de penetração total de geometria simples em chapas, tubos e vasos, onde tanto a solda quanto o metal de base são de aço de baixa liga. Quando especificado e apropriado, o ToFD também pode ser usado em outros tipos de materiais que apresentem baixa atenuação ultrassônica.
Esta norma foi elaborada com base na EN 14751 e fornece diretrizes sobre as capacidades especificas e limitações de ToFD para detecção, localização, dimensionamento e caracterização de descontinuidades em juntas soldadas por fusão. A técnica ToFD é de geração de imagens ultrassônicas, a qual demonstra capacidade de detecção, localização e dimensionamento. Também é possível a caracterização de descontinuidades em uma certa extensão no metal de solda, assim como no metal de base adjacente.
O ToFD pode ser usado como técnica única ou combinado com outros métodos ou técnicas de END, tanto para inspeção de fabricação quanto para inspeção em serviço. Esta técnica, que é baseada na difração, bem como na reflexão, quando comparada as técnicas baseadas somente na reflexão, e menos sensível para a orientação da descontinuidade. Descontinuidades orientadas perpendicularmente a superfície, e nos ângulos intermediários de incidência, são detectáveis bem como descontinuidades na face da solda.
Quando especificado nesta norma, os parâmetros ultrassônicos estão referenciados ao aço que possui uma velocidade sônica de 5.920 m/s ± 50 m/s para ondas longitudinais, e 3.255 m/s ± 30 m/s para ondas transversais. Isto deve ser considerado quando se inspecionam materiais com velocidades diferentes. Em determinadas circunstâncias, como espessura, configuração da junta soldada, objetivo do ensaio, etc., é requerido mais que um único arranjo (montagem) ToFD. A imagem típica de ToFD tem em um eixo a componente tempo ou caminho percorrido pelo ultrassom e, no outro eixo, a distância percorrida pelos cabeçotes.
Devido a geometria V dos percursos ultrassônicos, a localização de uma eventual descontinuidade na direção da espessura não é linear. O ensaio ToFD deve ser realizado de forma correta e coerente, de modo que as imagens geradas sejam validas e possam ser avaliadas corretamente. Por exemplo, perdas de acoplamento e erros de aquisição de dados tem que ser evitados.
A interpretação das imagens ToFD requer inspetores com habilidade e experiencia. Algumas imagens de ToFD típicas de descontinuidades em juntas soldadas são apresentadas no Anexo B. Existe uma redução na capacidade de detecção de descontinuidades próximas ou conectadas com a superfície de varredura ou com a superfície oposta. Isto tem que ser considerado, especialmente para aços suscetíveis as trincas ou na inspeção em serviço.
Em casos onde é requerida total cobertura destas zonas, medidas adicionais devem ser tomadas. Por exemplo, ToFD pode ser acompanhado por outros métodos ou técnicas de END, como o ensaio de ultrassom pulso-eco. Sinais difratados de descontinuidades em soldas tem pequenas amplitudes comparáveis ao espalhamento causado pelos grãos grosseiros de alguns materiais, que podem dificultar a detecção e avaliação das descontinuidades.
A pessoa que executa o ensaio de ultrassom deve atender aos requisitos da NBR NM ISO 9712. Adicionalmente, os profissionais envolvidos com ToFD devem ter treinamento especifico no sistema de ultrassom ToFD utilizado, com certificação emitida pelo profissional nível 3 de ultrassom capacitado na técnica. O ensaio ToFD deve ser realizado de acordo com um procedimento escrito, que deve conter no mínimo os requisitos listados na tabela abaixo.

Todos os procedimentos de ensaio devem ser qualificados por profissional nível 3, de acordo com a norma especifica do produto, e as evidências da qualificação devem estar disponíveis para apreciação da contratante. A norma específica do produto pode ser uma norma de projeto, construção, fabricação, montagem e inspeção em serviço, que estabelece os requisitos técnicos referentes ao material, montagem e inspeção nos projetos de fabricação e construção de produtos ou equipamentos.
Quando não especificado na norma especifica do produto, a qualificação do procedimento deve ser efetuada em corpos de prova representativos do ensaio a ser efetuado. As características e a quantidade dos corpos de prova devem ser aprovadas pela contratante. Sempre que qualquer variável da tabela acima for alterada, deve ser emitida uma revisão do procedimento. Se a variável for essencial, o procedimento deve ser requalificado e revalidado.
Recomenda-se que o instrumento de ultrassom usado para a técnica ToFD seja calibrado de acordo com a NBR 15922, e os cabeçotes de ultrassom conforme NBR 16138, e realizados por laboratórios que atendem aos requisitos apresentados na NBR ISO/IEC 17025. Qualquer reparo ou manutenção no sistema de medição implica a necessidade de nova calibração, independentemente da periodicidade estabelecida. O item do sistema de medição que deve ser periodicamente calibrado e o bloco padrão deve ser realizado por laboratórios que atendem aos requisitos apresentados na NBR ISO/IEC 17025.
A periodicidade de calibração do bloco padrão depende da frequência e condições de utilização. Recomenda-se que a periodicidade de calibração atenda ao especificado na NBR ISO 10012. Qualquer avaria observada no bloco padrão implica na necessidade de nova calibração, independente da periodicidade estabelecida. O instrumento deve ser capaz de selecionar uma parte adequada da base de tempo dentro do qual os A-scan são digitalizados. Para selecionar esta parte adequada, deve-se ter uma janela com posição e comprimento ajustáveis.
O início da janela deve ser ajustável entre 0 µs e 200 µs do pulso transmissor e o comprimento da janela deve ser ajustável entre 5 µs e 100 µs. Desta forma, os sinais apropriados (onda lateral ou creeping, sinal do eco de fundo, um ou mais sinais de conversão de modo) podem ser selecionados para serem digitalizados e exibidos. Os sinais não retificados devem ser digitalizados com uma taxa de amostragem de pelo menos quatro vezes a frequência nominal do cabeçote.
A largura de banda do receptor deve no mínimo ter intervalo entre 0,5 e 2 vezes a frequência nominal do cabeçote a – 6 dB, a menos que certas classes de produtos e materiais específicos exijam maior largura de banda. Filtros de banda apropriados podem ser usados. O pulso de transmissão pode ser unipolar ou bipolar. O tempo de subida não pode exceder 0,25 vez o período correspondente a frequência nominal do cabeçote.
Para aplicações gerais, as combinações de instrumentos de medição de ultrassom e mecanismos de varredura (escaneres) devem ser capazes de digitalizar sinais com uma taxa de pelo menos um A-scan por 0,5 mm de comprimento escaneado. Para atingir este objetivo, a aquisição de dados e o movimento do mecanismo de varredura (escaner) devem estar sincronizados. Os A-scans digitalizados devem ser exibidos relacionando a amplitude aos níveis de cinza, plotados sequencialmente para formar uma imagem B-scan. O número de escalas deve ser de pelo menos 256 tons de cinza.
O instrumento de medição deve ser capaz de armazenar todas as imagens A-Scan na sua forma original, isto e, sem filtros de qualquer natureza, em uma mídia de armazenamento. Para fins de relatório, o respectivo software deve ser capaz de gerar cópias em papel das imagens A-scan e B-scan. O instrumento de medição deve ser capaz de realizar uma média de sinal (averaging).
Para atingir as configurações de ganho relativamente alto, necessárias para sinais típicos de ToFD, pode ser usado pré-amplificador, que deve ter uma resposta plana sobre a faixa de frequências de interesse. Este pré-amplificador deve ser posicionado tão próximo quanto possível do cabeçote receptor. Os cabeçotes ultrassônicos utilizados na técnica de ToFD devem atender pelo menos aos seguintes requisitos: número de cabeçotes: 2 (transmissor e receptor); modo de onda: ondas longitudinais.
O uso de cabeçotes de ondas transversais pode ser empregado em situações especificas de forma a completar as longitudinais. Ambos os cabeçotes devem ter a mesma frequência nominal. A frequência central deve estar dentro de uma tolerância de ± 10% da frequência nominal e o comprimento de pulso tanto da onda lateral quanto do eco de fundo não pode exceder dois ciclos, medidos a 10 % do pico da amplitude (queda de 20 dB);
A distância entre a superfície de ensaio e a superfície de contato do cabeçote não pode exceder 0,5 mm. Para superfícies cilíndricas e esféricas, este requisito e atendido com a seguinte equação: D = 15 a, onde D é o diâmetro do componente, expresso em milímetros (mm); a é a dimensão da sapata do cabeçote na direção do ensaio, expressa em milímetros (mm). Se o requisito especificado não for atendido, uma sapata deve ser adaptada à superfície de contato do cabeçote e a sensibilidade e a escala devem ser ajustadas adequadamente.
Os mecanismos de varredura devem ser usados para manter uma distância constante e alinhamento entre os pontos de saída dos cabeçotes. Uma função adicional dos mecanismos de varredura e fornecer aos instrumentos de ultrassom informações de posição dos cabeçotes, sendo capaz de gerar a posição relacionada as imagens. Informações sobre a posição dos cabeçotes podem ser fornecidas por meio de, por exemplo, codificadores incrementais magnéticos ou óticos ou potenciômetros.
Os mecanismos de varredura no ToFD podem ser motorizados ou acionados manualmente. Eles devem ser guiados de maneira adequada, como cinta de aço, cinto, sistemas de rastreamento automático, rodas guiadas etc. A exatidão na orientação em relação ao centro de uma linha de referência, por exemplo, a linha de centro da solda, deve ser mantida dentro de um erro máximo admissível de ± 10% da separação entre os pontos de saída dos cabeçotes.
As inspeções devem ser realizadas de acordo com o procedimento qualificado, que deve conter o plano de varredura a ser utilizado, conforme as especificações técnicas aplicáveis. Para inspeções de fabricação, o volume de ensaio e definido como a zona que inclui solda e metal de base por pelo menos 10 mm de cada lado da solda, ou a largura da zona afetada pelo calor, o que for maior. Em todos os casos, o ensaio deve cobrir o volume total da região de interesse.
Para inspeção em operação, o volume de ensaio pode ser direcionado para áreas de interesse especifico. Os cabeçotes devem ser ajustados para garantir uma cobertura adequada e condições ideais para iniciar e detectar os sinais difratados na área de interesse. Para soldas de topo de geometria simples, onde a largura da solda e estreita na superfície oposta à da varredura, o ensaio deve ser realizado com uma ou mais configurações, dependendo da espessura da parede.
Deve-se tomar cuidado para escolher as combinações de parâmetros adequadas. EXEMPLO Na faixa de espessura de 15 mm a 35 mm com frequência de 10 MHz, um feixe com angulo de 70° e um cristal de tamanho de 3 mm pode ser apropriado para uma espessura de 16 mm, mas não para 32 mm.
O planejamento de ensaios de geometrias complexas, como juntas de espessuras diferentes, juntas de angulo ou bocais, requer profundo conhecimento da propagação sônica, blocos de referencia representativos e softwares específicos, e este planejamento está além do escopo desta norma. As áreas de varredura devem permitir que o volume do ensaio seja totalmente coberto. Elas devem ser uniformes e livres de corpos estranhos que possam interferir com o acoplamento do cabeçote, como corrosão, escamação, respingos de solda, entalhes e ranhuras.
As ondulações na superfície de ensaio não podem resultar em uma diferença entre cabeçotes e a superfície de ensaio maior que 0,5 mm. Estes requisitos devem ser assegurados pela preparação adequada da superfície para a inspeção, se necessário. As áreas de varreduras podem ser consideradas satisfatórias se a rugosidade da superfície, Ra, não for maior do que 6,3 µm para superfícies usinadas, ou não superior a 12,5 µm para as superfícies jateadas.
Ao usar cabeçotes e acoplastes convencionais, a temperatura da superfície do ensaio deve estar na faixa de 0 °C a 50 °C. Para temperaturas fora deste intervalo, a compatibilidade do cabeçote e do acoplam-te deve ser verificada durante a qualificação do procedimento. Para gerar imagens adequadas, deve-se utilizar um acoplante que forneça uma transmissão de ultrassom constante entre os cabeçotes e o material. O acoplante utilizado para ajuste deve ser o mesmo que o utilizado nos ensaios subsequentes e ajustes posteriores.
Para assegurar a repetitividade do ensaio, um sistema de referência permanente deve ser aplicado. Recomenda-se inspecionar o metal de base antes de realizar o ensaio ToFD (normalmente utilizado ultrassom com cabeçotes normal ou de duplo cristal), pois a presença de descontinuidades no metal de base adjacente a solda pode ocasionar áreas obscurecidas ou dificuldades na interpretação dos dados.
Caso sejam detectadas descontinuidades no metal de base durante o ensaio ToFD, deve-se inspecionar o local com cabeçote normal ou de duplo cristal. Um bloco de referência deve ser utilizado para determinar a adequação do ensaio, como cobertura, ajuste de sensibilidade, entre outros. As recomendações para blocos de referência são apresentados no Anexo A.
O bloco de referência deve ser fabricado de material equivalente a peça ensaiada (por exemplo, no que diz respeito a velocidade sônica, estrutura de grãos e condição superficial). A espessura do bloco de referência deve ser representativa para a espessura da peca ensaiada. Portanto, a espessura deve ser limitada a um valor mínimo e máximo em relação a espessura do objeto de teste. Recomenda-se que a espessura dos blocos de referência esteja entre 0,8 e 1,5 vez a espessura da peça ensaiada com uma diferença máxima na espessura de 20 mm em relação ao objeto de teste.
Deve-se evitar que o eixo (linha central) entre os cabeçotes não tenha angulo menor que 40° na parte inferior do bloco de referência. A espessura mínima do bloco de referencia deve ser escolhida de tal forma que o ponto de interseção do feixe da configuração escolhida esteja sempre dentro do bloco de referência. O comprimento e a largura do bloco de referência devem ser escolhidos de modo que todos os defeitos artificiais possam ser devidamente detectados.
Para os ensaios de soldas longitudinais em componentes cilíndricos, blocos de referencia curvos devem ser utilizados com diâmetros entre 0,9 e 1,5 vez o diâmetro do componente. Para os componentes com diâmetro maior ou igual a 300 mm, um bloco de referência plano pode ser usado. Para uma espessura entre 6 mm e 25 mm são necessários pelo menos três refletores. Para espessura maior que 25 mm, são requeridos pelo menos cinco refletores. Refletores de referência típicos são furos laterais e entalhes.
Os dois cabeçotes executam a varredura paralelamente a solda com orientação e distância fixa em relação a linha central da solda. Os dados coletados durante uma varredura podem ser usados para fins de detecção e dimensionamento. Para a avaliação especifica das indicações detectadas durante a varredura inicial, varreduras adicionais podem ser necessárias, como, por exemplo, varreduras descentralizadas, varreduras perpendiculares a descontinuidade ou configurações de ToFD complementares.
Por fim, pode-se dizer que a avaliação e o critério de aceitação se baseiam na análise dos sinais ultrassônicos transmitidos, refletidos e difratados dentro de uma imagem ToFD. Após a classificação de todas as indicações relevantes e determinação da sua localização e tamanho, as indicações devem ser avaliadas segundo critérios e níveis de aceitação especificados, respectivamente. O critério de avaliação e o registro de descontinuidades deve estar de acordo com a norma especifica do produto e/ou especificações de projeto. Para inspeção em serviço, o critério de aceitação deve ser aquele indicado pela contratante.
Com base nesta avaliação, as indicações podem ser classificadas como aceitáveis ou não aceitáveis. Se o critério de aceitação especificado exigir detecção de um determinado tamanho de descontinuidade, tanto numa superfície quanto em ambas superfícies da solda, isto pode exigir o uso de técnicas ou métodos fora do escopo desta norma.