A disseminação da cultura da segurança de processo na indústria
Redação
As constatações recentes de acidentes catastróficos no mundo conclamam toda a comunidade do Planeta para uma reflexão urgente e de extrema importância de todos os profissionais, principalmente para os gestores das empresas, no sentido de direcionarem os seus objetivos para a disseminação da cultura de segurança de processo em suas instalações de produção. Esta convocação baseia-se a partir de constatações de incidentes e falhas ocorridas não só em procedimentos como também em equipamentos operacionais e conduta humana pertencentes a um complexo industrial, e que necessitam constantemente de uma governança sobre as suas gestões de segurança.
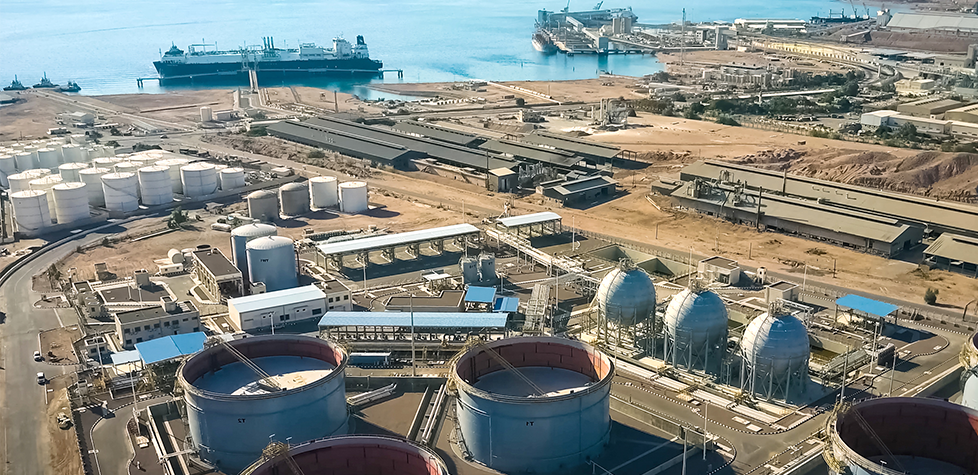
Silvio L. Valença e Gabriela O. Valença -
No mundo atual, é notória a busca entre os países sejam eles já industrializados, como também os ditos emergentes, para alcançarem um processo de industrialização acelerado no mais curto espaço de tempo possível, com a finalidade de obter enormes benefícios econômicos, tais como: aumento da renda per capta e melhor nível de vida para a população. Por sua vez, a indústria tem vivido momentos de reflexão no sentido de aprimorar as questões de prevenção de perdas de processo que minimizem os impactos nas pessoas, instalações e ao meio ambiente.
Há décadas, impulsionados por uma cultura e uma legislação que de certa forma exigem a prevenção de acidentes ocupacionais, as empresas investiram na busca de redução de acidentes com as pessoas no ambiente de trabalho, através da elaboração de procedimentos, análises de risco, especificação de Equipamento de Proteção Individual (EPI) e outras iniciativas que buscassem identificar os riscos e medidas de controle, que pudessem reduzir as possibilidades do trabalhador se acidentar na execução das tarefas. Estas iniciativas às vezes impunham aspectos de condições ou contextos que criam ao trabalhador dificuldades para realização do trabalho, com isso, como estes não têm uma cultura prevencionista incorporada, geram-se improvisações nas etapas do trabalho com riscos de acidentes.
Percebeu-se, com o passar dos tempos, que conquistas foram alcançadas nas reduções dos acidentes de trabalho e de certa forma, principalmente a indústria petroquímica registra melhorias contínuas nesta área ao longo dos anos. Porém, se fizermos uma reflexão no sentido de se identificar quais e em que abrangência se evoluiu nas questões de prevenção e formação cultural em gestão de riscos de processo, identificamos uma grande lacuna a ser conquistada.
Percebe-se em algumas organizações, uma cultura em que se acha que quem deve mais conhecer o processo e seus riscos são as pessoas que trabalham na operação, como também na área de segurança. Neste contexto, os recentes acidentes de processo demonstraram que a não existência de um programa sistêmico de transferência de conhecimento de processo, que assegure o envolvimento, capacitação e descentralização das questões associadas a gerenciamento de riscos de processo, fará com que a indústria não consiga reduzir o número dos grandes acidentes industriais que tem o potencial de causar muitas fatalidades aos trabalhadores e comunidade.
O objetivo que deve ser conquistado pelas organizações é através da descentralização planejada e do conceito de responsabilidade de linha. Assim devesse criar na organização, um entendimento do seu papel e responsabilidades na prevenção de acidentes de processo.
Em contrapartida, a cultura anteriormente disseminada com relação à segurança, o avanço tecnológico que vem acontecendo em todo mundo, tem influenciado diretamente no crescimento industrial. Isto é especialmente verdade na indústria química e petroquímica, que estão na era de processos mais complexos, ou seja, processos que envolvem condições críticas de pressão e temperatura, meios reacionais, dentre outros, cujos acidentes (relacionados ao processo) podem levar a grandes perdas e são potencialmente capazes de comprometer a sustentabilidade da organização.
Com o propósito de se obter níveis cada vez maiores de segurança nas instalações industriais, tem-se sugerido a utilização de um sistema de gestão, capaz de garantir a harmonia na utilização dos recursos disponíveis e que seja efetivo na prevenção de perdas. Este sistema de gestão em segurança de processo ajuda as pessoas envolvidas – gerentes, operadores, engenheiros e contratados, que trabalham na indústria – a realizarem suas atividades com mais segurança.
No entanto, a existência de um sistema de gestão por si só, não garantirá pleno controle da segurança de processo. De acordo com Pitblado (2008), as estatísticas publicadas pela USA EPA RMP-Star mostram que sistemas de gestão em segurança de processo têm gerado um modesto incremento desta nas instalações industriais. Também, segundo Pitblado (2008), se recomenda fortemente uma completa integração entre o sistema de gestão em segurança de processo e um programa de integridade mecânica, com foco nas barreiras de proteção (salvaguardas), conduzido por um vasto processo de análise de risco, desde o projeto até a operação.
Desta forma, uma abordagem a ser considerada para o efetivo controle da segurança de processo deve prever a implantação de um sistema de gestão concebido para devotar especial atenção ao gerenciamento/manutenção do nível de integridade requerido às barreiras de proteção, comumente denominadas salvaguardas, as quais têm potencial para proteger as pessoas, o meio ambiente e a propriedade, de consequências indesejadas, seja prevenindo acidentes, ou seja mitigando seus efeitos.
As evidências de acidentes catastróficos mundiais neste exato momento, convocam para uma reflexão urgente e de extrema importância de todos os profissionais, principalmente para os gestores das empresas mais bem organizadas, no sentido de direcionarem os seus objetivos para disseminação da cultura de segurança de processo em suas instalações de produção. Esta convocação baseia-se a partir de constatações de incidentes e falhas ocorridas não só em procedimentos como também em equipamentos operacionais e conduta humana de um complexo industrial, e que necessitam constantemente de uma governança sobre as suas gestões de segurança.
É notório que, nos últimos anos, em diversas empresas do parque industrial no Brasil, houve um trabalho generalizado no sentido de divulgar e sensibilizar todos os trabalhadores com relação à segurança pessoal, como por exemplo, o uso de Equipamento de Proteção Individual (EPI) e Equipamento de Proteção Coletiva (EPC), onde obviamente sensibilizou a maioria desses que compõem as forças de trabalho com relação evidentemente aos efeitos provocados em cada indivíduo pelos riscos provenientes de diversas fontes identificadas nos locais de trabalho.
No entanto, o trabalhador equipado e protegido com relação aos riscos pessoais enaltece a conscientização humana por meio da cultura de segurança dentro de uma instituição. Todavia, a vigília e gestão para assegurar e garantir o funcionamento de uma planta operacional em perfeitas condições de tolerabilidade exigida e determinada através dos Estudos de Análise de Riscos (EAR), requer vários outros meios para efetuar o gerenciamento das observações citadas nesses EAR.
A ideia inicial para alavancar a necessidade de uma atenção maior voltada para as problemáticas inerentes aos incidentes e acidentes de processo, passa justamente por massificar a divulgação através das gerências operacionais com toda a sua força de trabalho seja ela própria ou contratada, no sentido de apresentar por meio dos alertas de segurança as ocorrências funestas das diversas áreas industriais com plantas de processo.
Utilizando uma metodologia, a qual se norteia pela premissa básica de que nem todos os riscos são iguais ou podem causar as mesmas consequências. Princípio este respaldado em notações de que perigos/riscos pessoais ou ocupacionais tais como escorregões, quedas, cortes e acidentes com veículos, geralmente produzem efeitos em um único trabalhador.
Por outro lado, os perigos/riscos de processo em uma unidade fabril podem ocasionar acidentes maiores, envolvendo a liberação de materiais potencialmente perigosos, incêndio e explosões ou ambos. Os incidentes de segurança de processo podem ter efeitos catastróficos e podem resultar em múltiplas mortes e feridos, assim como danos substanciais a economia, a propriedade e ao ambiente.
Incidentes de segurança de processo podem causar dano, tanto aos trabalhadores no interior da fábrica, como ao público que reside nas vizinhanças. Esta é, portanto, a razão pela qual consolidamos em nossa metodologia da prática de visitas aspectos referentes à gestão de segurança de processo, onde a mesma está focada no projeto e engenharia de instalações, análises de perigos e riscos, investigação de incidentes, gestão da mudança, inspeção, testes e manutenção de equipamentos, alarmes e controles de processo eficazes, procedimentos de operação e manutenção, formação de pessoal e fatores humanos.
Diante das necessidades com relação ao atendimento cada vez mais frequente das aplicações de práticas operacionais voltadas para a segurança operacional de processo, torna-se necessário a elaboração de um plano de ações para conhecimento das gerências operacionais da empresa. A implantação dessa prática de visitas deverá ser discutida e aprovada em reunião do Comitê das Gerências em todos os níveis hierárquicos de uma companhia.
Essa prática consiste inicialmente da elaboração de uma sistemática de itens de verificação sobre segurança de processo, onde previamente a equipe multidisciplinar de profissionais estabelece uma lista de sistemas, equipamentos e procedimentos necessários para cumprimentos das exigências pertencentes ao sistema de gestão de segurança operacional das Diretrizes de SMS (Segurança, Meio Ambiente e Saúde) da companhia; justamente por meio de uma matriz correlacionada com as atividades e instalações da área a ser visitada, evidentemente com maior destaque para as recomendações inerentes a segurança de processo. Em uma ação já estabelecida anteriormente, a gerência operacional responsável pelas instalações, disponibiliza um cronograma de visitas estabelecendo datas e responsáveis para acompanhamento de informações solicitadas, como também do apoio logístico para realização dos trabalhos.
15 dias antecedendo a visita é feita formalmente a solicitação das documentações da área, a exemplo dos desenhos da planta de localização da área, planta de localização dos equipamentos, fluxograma de processo, estudos de análise de riscos, registros das últimas mudanças ocorridas nas instalações, planta baixa de classificação de áreas, descrição das características da área, etc. Em seguida, após o recebimento destes documentos, é feita a análise detalhada das informações e verificação de conformidade in situ durante a visita pelos técnicos da equipe multidisciplinar juntamente com os membros da gerência de operação envolvidos com o desenvolvimento dos trabalhos.
No ato da visita propriamente dita da área, é feita uma abordagem com todos os presentes, sobre a necessidade de se estabelecer fortemente uma cultura dentro da companhia sobre os aspectos que dizem respeito à segurança de processo das instalações, mencionando inclusive exemplos de catástrofes já ocorridas e que possuem equipamentos e sistemas semelhantes daquela unidade fabril. Depois, os profissionais capacitados e responsáveis pelas disciplinas de segurança, integridade e processo passam a desenvolver as suas atividades, verificando e analisando os pontos vulneráveis de risco e o comprometimento da funcionalidade segura das instalações.
Imediatamente diante de uma constatação de irregularidade no cumprimento a segurança de processo, é provocada uma reunião no local da evidência por meio de todos os envolvidos pela atividade e apontada a necessidade de uma intervenção seja ela de imediato ou programada, dependendo do nível de gravidade da irregularidade constatada pelo analista do grupo de visitantes. Todas as evidências comprovadas, como não conformidades, passam a ser notificadas em relatos escritos e também através de fotos, para subsidiar posteriormente a elaboração do relatório de visita, seguindo uma sequência resumida da sistemática adotada para tratamento do risco pelo grupo da área envolvida na visita, conforme apresentada na Figura 1.
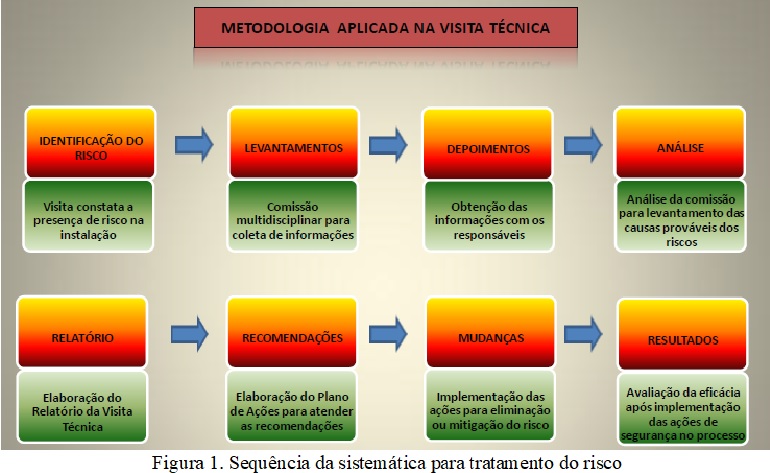
Uma vez concluída a verificação de todas as áreas de processos na instalação, todos os envolvidos na visita técnica participam de uma reunião coordenada pelo líder da equipe multidisciplinar. Nessa oportunidade ressalta-se com maior ênfase a abordagem dos fatos mais críticos inerentes à segurança de processo, a exemplo de: vazamentos em equipamentos, tubulações e acessório, equipamentos sem a presença de instrumentos de controle de variável operacional, tubulações de drenos e suspiros sem a utilização de tampões, flange de conexões faltando parafusos, falta de fixação de equipamentos na sua base, falta de identificação dos equipamentos e tubulações, presença de sistemas de inibição (by pass) sem tratamento por estudo de análise de risco ou hazop, etc.
Por conseguinte, o grupo de técnicos, que compuseram a equipe da visita técnica, providencia a elaboração do Relatório de Visita Técnica da Unidade, e o envia para a gerência operacional, no sentido de efetuar o atendimento as não conformidades registradas no mesmo. Contudo, a gerência de operações de posse desse relatório providencia o registro através de planilhas com os itens mencionados para atendimento das não conformidades, inclusive efetuando abrangência nas demais instalações de produção referentes a estas observações de riscos de processos por meio de comunicados de alerta de segurança, além de elaborar uma rotina de controle para gestão das ações de melhorias solicitadas pelos membros da equipe de visita.
Em resumo, podemos concluir que será perceptível pelas gerências operacionais, mediante a ideia surgida e a consolidação da prática de visitas periódicas em instalações de uma companhia, a presença e desenvolvimento de uma disseminação da cultura de segurança de processo com a força de trabalho Isso permite uma melhoria referente as inspeções tanto dos sistemas como dos equipamentos e procedimentos de processo, onde por meio desta prática espera-se atingir um controle mais seguro dos processos no segmento de cada unidade fabril.
Essa cultura visando à segurança de processo obviamente estabelece o comprometimento do empregado para consigo, e para os seus semelhantes nos respectivos locais de trabalho, dirimindo o surgimento de atos inseguros, como também de condições inseguras, as quais resultam nos indesejáveis acidentes, perdas, danos, riscos ou quase acidentes. Por fim, gostaríamos de deixar claro que as questões de segurança de processos não podem ser tratadas através de programas isolados, ou seja, dissociados entre si.
Deve-se buscar a implantação de um sistema de gestão que seja inserido no âmbito estratégico da organização. Perdas em segurança de processos podem trazer grandes catástrofes e até promover o fechamento de uma organização.
Agradecimentos
Agradecemos à Petrobras - Petróleo Brasileiro S/A por proporcionar e incentivar o desenvolvimento para aprendizados nas suas diversas áreas de atuação, o que certamente enaltece não só os seus profissionais quanto à qualidade técnica, como também do reconhecimento das suas tecnologias aplicadas no ramo energético em diversas localidades do mundo.
Referências
AEA TECHNOLOGY. Major Hazardous Incident Data Service – MHIDAS. Harwell. 1980. Base de Dados em DB. Versão 2005.
BIRD, FRANK E. & LOFTUS, ROBERT G. Loss Control Management, Institut Press, USA, 1976.
CENTER FOR CHEMICAL PROCESS SAFETY. Guidelines for Engineering Design for Process Safety. 1 ed. New York: AIChE, 1993.
CENTER FOR CHEMICAL PROCESS SAFETY. Layers of Protection Analysis - SIMPLIFIED PROCESS RISK ASSESSMENT. 1 ed. New York: AIChE, 2001.
CENTER FOR CHEMICAL PROCESS SAFETY. Process Safety Leading and Lagging Metrics - You don't improve what you don't measure. Inicial Release. New York: AIChE, 2007.
CROWL, Daniel A., LOUVAR, Joseph F. Chemical Process Safety – Fundamentals with Applications. 2.ed. Upper Saddle River, New Jersey: Prentice Hall PTR, 2001.
LEES, F. P. Loss Prevention in the Process Industries. vol. 1 e 2, London, 2ª ED. Ed. Butterrworts, 1996.
MAH, R. S. H. Chemical processes structures and information flows, Butterworth Publishers, 1990.
OSHA, Occupational Safety & Health Administration - Process safety management of highly hazardous chemicals – 29 CFR 1910.119, 1992.
PITBLADO, Robin. Global Process Industry Initiatives to Reduce Major Accident Hazards. In: I Seminário do Comitê de Fomento Industrial do Pólo Petroquímico de Camaçari (COFIC) 9-13 out. 2008, Salvador.
REASON, James. Human error: models and management: British Medical Journal, Manchester, 18mar.2000, Education and Dabate. 320, p. 768-770.
SUTTON, Ian S. Process Safety Management. 2.ed. Houston, Texas: Southwestern Books, 1997.
TREVOR, Kletz. What Went Wrong? 5.ed. Butterworth Heinemann, Jun-2009.
U.S. DEPARTMENT OF ENERGY. DOE-HDBK-1101-2004: DOE Handbook Process Safety Management For Highly Hazardous Chemicals. 1 ed. Washington: DOE, 2004.
WEELS, G.L. Safety in Process Plant Desing.George Godwin, London, 1980.
Silvio L. Valença é doutor e engenheiro mecânico e de segurança do trabalho da Petrobras S/A silviovalenca@bol.com.br; e Gabriela O. Valença é acadêmica, engenharia de meio ambiente e sanitária na Universidade Federal de Sergipe (UFS) - v.oliveira.gabi@gmail.com
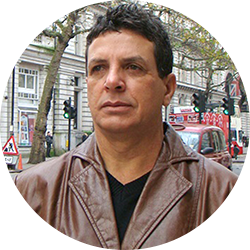
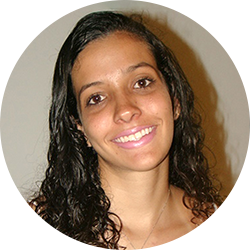